
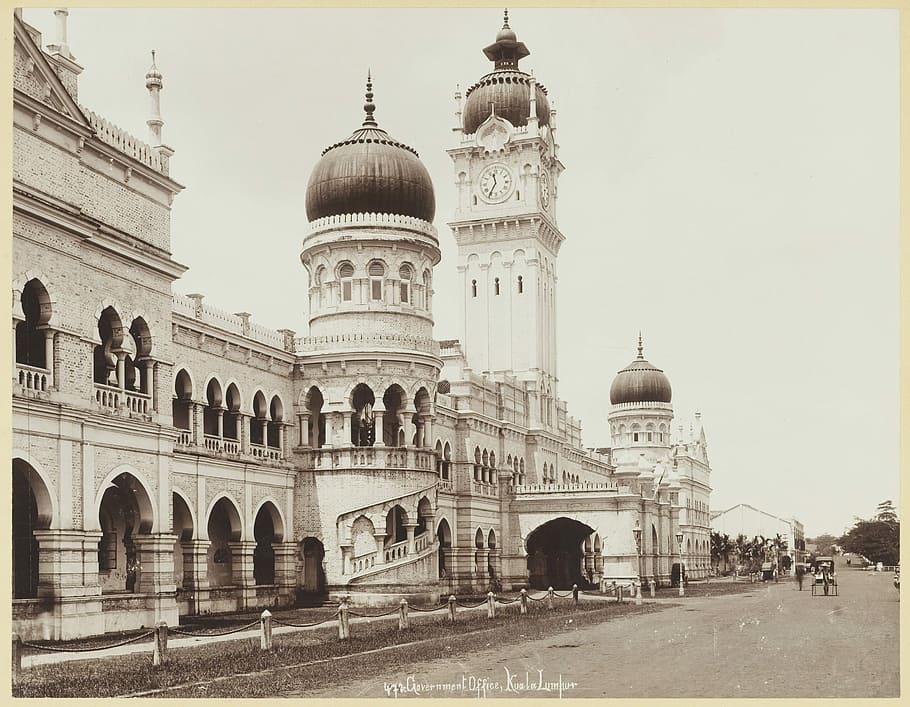
Lead numbers are placed at fixed intervals along the plate adjacent to the weld or around the circumference of a pipe to enable the position of any imperfections to be accurately located. Radiography of flat plates and cylinders large enough to permit entry for placement of the film is a relatively simple operation, as shown in Fig. The light itself should be white and diffuse and there should be as little light as possible leaking around the edges of the radiograph. The luminance of the viewing screen will need to vary with the density of the radiograph – there is generally a rheostat control (a dimmer switch) on the viewer to enable the luminance to be varied. Viewing should be carried out in a darkened room, allowing a period of time for the viewer’s eyes to be accustomed to the conditions. Many application specifications require such individuals to be independently certified to a suitable certification scheme such as PCN, administered by the British Institute for NDT or CSWIP, administered by TWI Certification Ltd. In addition to being fully conversant with radiographic techniques such individuals should also have a comprehensive knowledge of welding processes, joint design and the various imperfections that may occur. Interpretation of the radiographs must be undertaken by trained and experienced radiographers. Care must be taken to ensure that there is no light contamination, the processing chemicals are at the correct concentrations and temperatures and that drying the film does not leave marks and stains that would leave spurious indications and would make accurate interpretation difficult. The sensitivity measured by the use of a wire IQI is not the same as the sensitivity using a step wedge IQI.Īs with any film, the method of processing will affect the quality of the image. The diameter of the smallest hole visible on the radiograph determines the sensitivity, this being calculated as hole diameter divided by component thickness expressed as a percentage. As with the wire IQI, the material and dimensions of the step wedge are selected to match the application.
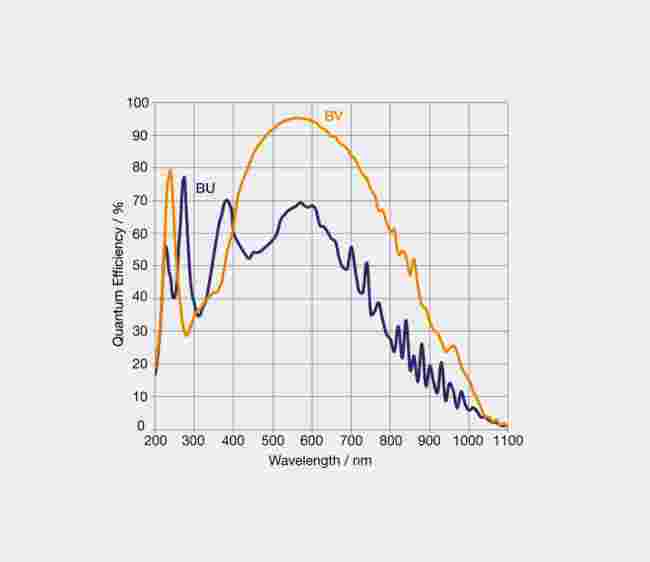
It is a stepped wedge with a hole drilled in each step, the hole diameter matching the thickness of the step. The step hole IQI is used less frequently. Alternatively an actual wire diameter that must be visible is specified. Most application codes specify a sensitivity of between 2-4% this is a maximum, the smaller the figure the greater the sensitivity of the radiograph. The sensitivity is taken as the smallest diameter wire that can be seen divided by the component thickness, expressed as a percentage. Ideally the IQI is placed on the source side of the component and, in the case of a weld, transversely across the joint although this is not always possible when radiographing pipe and tube butt welds. National Structural Integrity Research CentreĬlick here to see our latest technical engineering podcasts on YouTube.Structural Integrity Research Foundation.
